An example could be adding sensors and monitoring our products in real time. Then, we not only use the data to analyse the design but also predict failure and time maintenance schedules. Manufacturing techniques are also changing. Customers want strong, proven, lightweight and easily maintained components whilst keeping to a low cost. Here, the new manufacturing capabilities such as additive manufacturing help us innovate our designs.
Machines and products are becoming intelligent
The fourth industrial revolution is upon us: machines infused with intelligence.
Markus Lorenz, Partner and Managing Director of the Boston Consulting Group in Munich, has estimated that this transformation will completely change the way manufacturing works today, making it 30% faster and 25% cheaper, because a machine will know when it makes a mistake and correct itself.Nowadays, standardisation and automation are key factors in most companies’ design strategies, and these could be seen as the first steps towards creating intelligent machines and products. This wasn’t necessarily the case a few years ago. The oil and gas industry has had standardised CAD for many years, although projects tended to be treated as one-offs with minimal design standardisation. A growing trend in this industry is to reduce costs by modularising designs, with the aim of generating a core 80% of the project using standard modules, leaving engineers to focus on the final 20%.Automation is another change in this sector. There has been strong focus on becoming leaner and doing more with less. This means looking at the workflows and working out what can be removed, reduced or automated.
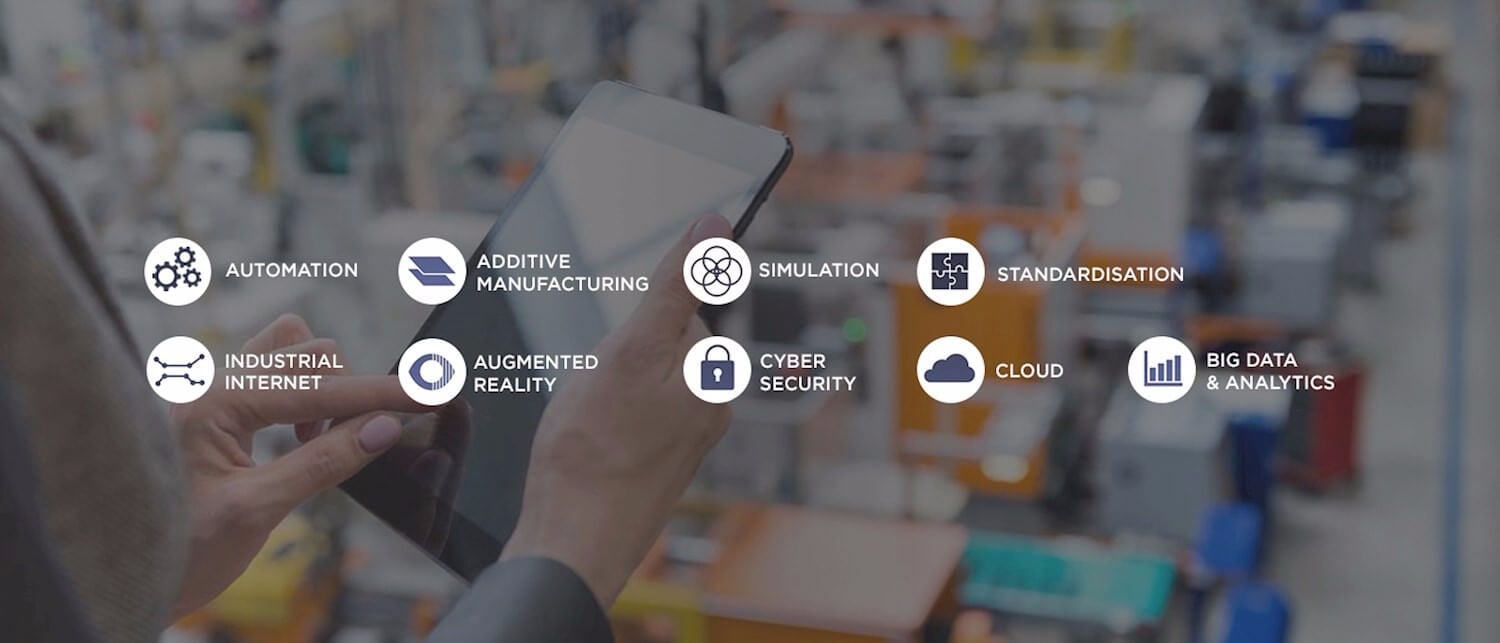
Internet of Things. Advanced manufacturing. Standardisation.
Automation. Data management.
These key areas free up more design time around the company so engineers can design better products and focus on the bespoke work for each contract. This modern-day approach is something we can all learn from and apply no matter what our industry or size. This also means that there will be changes in the engineer’s job description, and the manufacturing jobs of the future will require completely new manufacturing skills. One way is to acknowledge this and embrace the change by using it as a competitive advantage for companies in the future.
Start small –Think big
Think about the processes you have in your company and pick one to work on. The best way to start is to consider tasks that are repetitive, fairly stable, have low complexity and are wasteful. Ask yourself questions like: Do we need to do this process? Who uses the outputs and why? What would be the savings of improving by 50, 60, 80 or 100 per cent? And you are on your way to making a change and increasing your product quality to attract new and more customers.
At Symetri, we help our customers across Northern Europe to remove redundancy from their processes to create more value and increase productivity. Our consultants have vast experience working in all these disciplines and will be happy to share their knowledge and get you on the path to a leaner future.